Point de vue sur l'aluminium comme matériau de construction, par Simon Aubry et Bernard Vaudeville
Point de vue sur l'aluminium comme matériau de construction, par Simon Aubry et Bernard Vaudeville, paru dans AMC spécial Alu en juillet 2008.
AMC: L’aluminium est un matériau encore jeune et qui n’a vraiment pris une place dans la construction que depuis la dernière guerre mondiale. Et pourtant certains voudraient déjà le condamner pour des raisons de défense de l’environnement. N’est-ce pas aller un peu vite. Et peut-on vraiment se défaire d’un matériau aux qualités si particulières. ?
Simon Aubry : La question c’est celle de la relation de l’aluminium à l’énergie. C’est un fait : transformer la bauxite, qui est un oxyde, en métal pur exige un investissement énergétique important . En contrepartie, l’aluminium est un matériau économique à recycler : pour en produire une tonne à partir de déchets, il ne faut que 5% de l’énergie nécessaire à la production initiale d’une tonne à partir du minerai. Cela tient à deux caractéristiques de l’aluminium : son point de fusion est bas et il reste pur car il ne s’oxyde pas. Deux différences par rapport à l’acier. C’est un des matériaux les plus rentables à recycler, ce qui explique son taux de recyclage exceptionnellement élevé.
Bernard Vaudeville : Peut-être qu’avant même de débattre de ses qualités ou limites environnementales, il faut souligner ses performances mécaniques et sa résistance à la corrosion, qui sont certainement ses qualités principales. La Maison de la Radio à Paris est un bel exemple des qualités de durabilité de l’aluminium. C’est un bâtiment qui a 45 ans et dont les panneaux qui l’habillent sont impeccables. Aujourd’hui les habillages sont plus légers : utilisés pour écrans, volets mobiles, des filtres. Mais leur aspect bougera peu avec le temps. L’aluminium offre aussi un très bon rapport résistance-poids. C’est un matériau très adapté aux structures légères, au sens physique du terme. Il n’est sur ce point dépassé que par le titane et des matériaux composites à base de fibres de carbone. C’est pourquoi l’aluminium est utilisé par des industries ou sur des objets pour lesquels la question du rapport résistance-poids est importante: l’aéronautique, les transports en général.
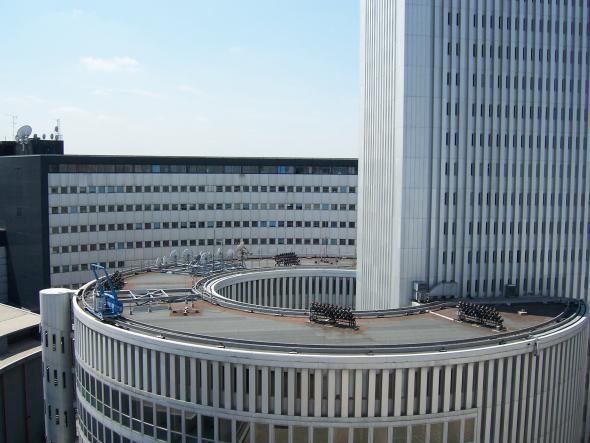
La Maison de la Radio, inaugurée en 1963, utilise l'aluminium pour ses façades (menuiseries, bardage, brise-soleil...).
AMC : Mais dans le bâtiment, quel est l’intérêt de la légèreté, au sens physique du terme ?
B. V. A première vue, la question se pose assez peu, puisque l’on peut se permettre que les bâtiments soient relativement lourds. Mais dans certaines situations particulières, la légèreté devient intéressante. C’est le cas de la structure qui doit couvrir des fouilles archéologiques à Bibracte, sur laquelle nous travaillons (RFR + T/E/S/S) actuellement avec Paul Andreu, et qui devrait être bientôt réalisée. C’est une structure de 30 mètres de portée environ, mais qui doit être facilement montable et démontable sans engin de levage lourd. Le critère de légèreté des éléments structurels est donc important. Et cette légèreté doit être alliée à la résistance.
Mais je crois qu’il ne faut pas considérer ces cas comme marginaux dans la construction. Nous pensons que ces cas vont devenir plus fréquents, et que vont se développer des architectures mobiles, des architectures démontables, des architectures flottantes…
Des situations aussi où la question de la surcharge sur un bâtiment existant ou au faîte d’un ouvrage se pose. Je pense précisément à une structure qui devait être en aluminium, car elle venait au sommet d’un paquebot construit à St Nazaire et que l’on devait en limiter le ballant.
AMC : Il s’agit dans ce cas de structures complètes, fabriquées en atelier et directement installées sur le chantier. On pense immédiatement à la tribune de presse du Lords Cricket Grounds à Londres.
B. V. : Cette coque en aluminium conçue par l’agence anglaise Future Systems est un magnifique exemple d’une des qualités de l’aluminium : la formabilité. Des coques de grande dimension, ayant des courbes complexes sont beaucoup plus difficiles à réaliser an acier. On retrouve aussi le fait que ces coques étant légères, elles peuvent être transportées plus facilement depuis l’atelier, jusqu’au site de leur installation. C’est aussi l’exemple des coques du restaurant « Georges » au 6ème niveau du Centre Pompidou à Paris, conçues par les architectes Jakob + MacFarlane avec RFR. Ces coques n’auraient pas pu être réalisées en acier dans cette continuité de forme. Dans ces exemples, il a été fait appel chaque fois aux industries des chantiers navals qui ont l’habitude de travailler avec l’aluminium et qui sont les plus à même de réaliser ce genre d’ouvrage. Travailler avec eux est intéressant car ils ont l’habitude des formes complexes et savent s’adapter, trouver la solution pour chaque cas particulier. Un bel exemple est la grande sculpture de l’artiste américain Frank Stella, mise au point elle aussi par RFR, réalisée en aluminium par les ateliers CMN à Cherbourg. Je ne pense pas qu’il y ait des entreprises de construction qui sachent mettre en œuvre de telles structures complexes.
Il y a bien sur une certaine mode architecturale qui pousse à ces formes complexes. Mais il y a aussi de plus en plus de situations où elles sont rendues nécessaires par le contexte. Et les concepteurs disposent aujourd’hui des outils de modélisation en 3D pour décrire les formes courbes et complexes. Hier il fallait être équipé de matériel de type industriel, aujourd’hui ces équipements sont tout à fait abordables. Et sont du reste de plus en plus utilisés par les agences d’architecture. Elles peuvent décrire formellement ce type de géométrie et ensuite les transmettre aux entreprises qui peuvent fabriquer directement à partir de ces mêmes données.
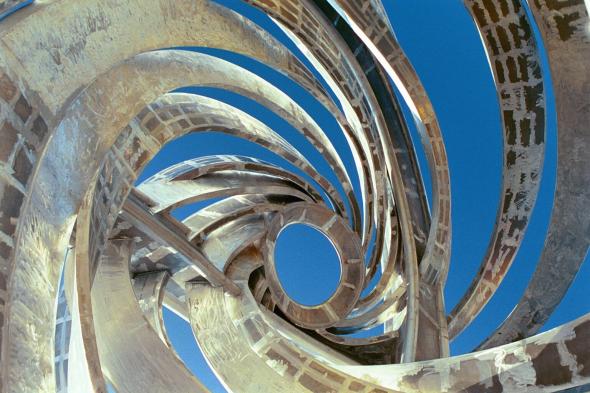
Le ruban en aluminium de 40 tonnes de la sculpture "Bandshell" de Frank Stella.
AMC : Est-ce qu’on peut imaginer des épaisseurs extrêmement fines dans le bâtiment, ne serait-ce que pour diminuer le coût ?
S.A. : Oui, il y a même l’exemple de la tôle aluminiée : une tôle-acier revêtue d’un dixième de millimètre d’épaisseur d’alu pour avoir l’aspect l’anti-corrosion de l’aluminium. C’est presque comme une sorte de peinture, de vernis, plus que comme une matière.
Ce qui est intéressant c’est qu’il y a des recherches actuellement pour combiner les matériaux.
B V : C’est aussi une des pistes de développement dans les années à venir, y compris dans le domaine de la structure. On ne conçoit plus la chose avec des matériaux simples mais utilisés dans des situations de composite. Qui permettent par exemple de lier d’une matière tout à fait solidaire l’aluminium et l’acier ce qui permet d’avoir la résistance de l’acier, ajouté avec la résistance à la corrosion de l’aluminium. C’est déjà utilisé dans les chantiers navals, éventuellement dans la construction aéronautique, mais c’est très méconnu dans le bâtiment. Cela permettrait de régler vraiment des problèmes qui ne sont pas forcément très visibles, des questions d’interface, de résistance à la corrosion de certaines zones, etc.
AMC : La malléabilité de l’aluminium, on la retrouve dans des pièces moulées. C’est très largement utilisé dans l’industrie, en particulier automobile, mais c’est plus rare dans le bâtiment, sauf pour de l’accastillage (poignées de portes etc.). Dans les années 60 on fait des panneaux de façades moulés, comme ceux de l’ambassade de France à Varsovie. Une solution qui n’a pas eu de suite. Je n’ai trouvé que deux applications d’applications très intéressantes dues à un même architecte autrichien.
B.V. : Le moulage ouvre un large champ d’application pour l’aluminium. On peut faire des choses formidables avec l’aluminium qu’on ne peut pas faire en acier. Il permet de réaliser des objets d’une finesse qui serait difficile à obtenir avec l’acier. Je pense aux grilles du magasin Louis Vuitton sur les Champs Elysées :120.000 pièces d’aluminium moulé, seul le moulage ayant permis d’avoir la finesse et la précision demandées. On a peut-être quelque chose comme 50.000 pièces assemblées dans une seule unité sans aucun joint de dilatation. On imagine les tolérances requises pour pouvoir le faire.
S.A. : Une autre manière d’exploiter la malléabilité, la ductilité de l’aluminium c’est l’extrusion.
C’est beaucoup plus performant qu’avec l’acier. On peut extruder de grandes longueurs, jusqu’à 12 mètres ou plus quelle que soit la section. Alors qu’avec l’acier, dès que la section est un peu importante, la longueur de production est limitée et nécessite de coûteux raboutages.
Et il y a une plus grande liberté pour la création de nouvelles filières. La tête d’une filière aluminium est en acier ordinaire, alors que pour extruder de l’acier, il faut une tête de filière en acier réfractaire spécial car elle doit résister à des températures bien plus élevées, à des pressions bien plus fortes.
AMC : À partir de quelle quantité est-il possible de créer son propre profil aluminium.
B.V. : Il faudrait vérifier ce chiffre, mais disons qu’à partir de 1000m2 de façade on doit pouvoir imaginer avoir son propre profil. Le coût fixe d’une filière aluminium est finalement assez bas.
Je trouve qu’il y a une certaine évolution des entreprises, alors qu’il y a encore quelques années c’était quasiment exclu. Sur un immeuble de bureaux que j’avais étudié avec RFR pour l’architecte Christian Devillers, sur la ZAC Rive Gauche à Paris, nous avons pu avoir une filière particulière pour les plaques formant brise-soleil.
Et répétons qu’on peut avoir un degré de précision exceptionnelle, de l’ordre du dixième de mm, qui évite les taraudages ultérieurs, des fixations mécaniques sans reprises, des clipsages précis.
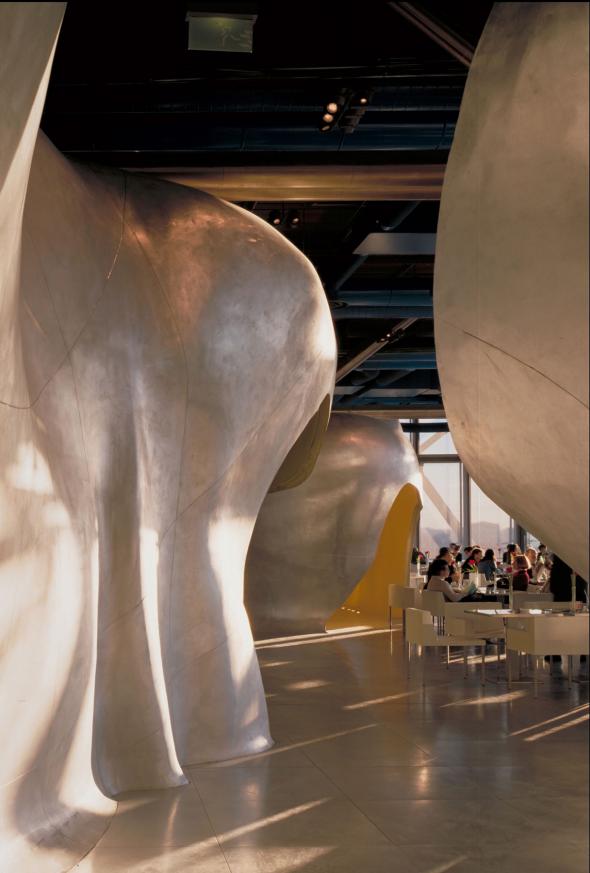
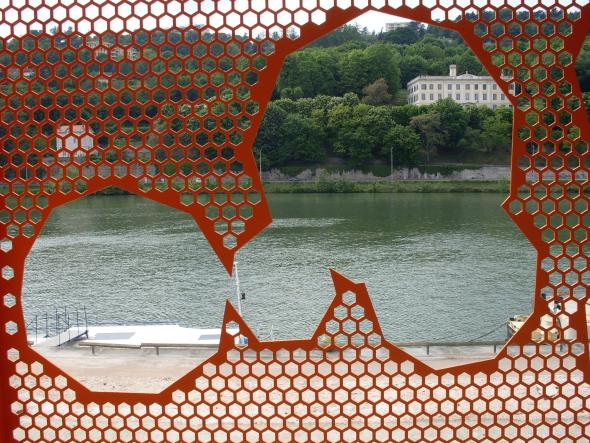
Les coques du restaurant "Georges" du Centre Pompidou et la résille du projet des Salins à Lyon.
AMC : À vous entendre, à côté des grands industriels classiques de l’aluminium, les façadiers, avec des produits de plus en plus performants, les concepteurs auraient à leur disposition tout un tissus d’entreprises – fondeurs, chaudronniers, chantiers navals – susceptibles de répondre à des demandes pointues.
B.V. : Plus que dans le domaine de l’acier, subsiste en France un tissu de transformateurs travaillants l’aluminium. Autour principalement des chantiers navals, de l’ameublement, de l’aéronautique. Et qui sont capables de répondre, avec une incontestable souplesse à des demandes particulières. Je pense à la sculpture de Frank Gehry dernièrement en quelques mois, en faisant appel à un fondeur d’art et à des soudeurs qui travaillent pour l’industrie aéronautique.
Ce sont des structures assez pointues mais petites parce que l’investissement pour travailler l’aluminium n’est pas très important, en particulier en raison de son bas point de fusion. Ce qui importe c’est la qualification du personnel. Par exemple un fondeur d’alu est à priori une entreprise beaucoup plus petite qu’un fondeur d’acier et cela permet d’avoir une qualité et une flexibilité caractéristique de l’artisanat.Y compris pour les chantiers navals : on trouve des entreprises qui travaillent sur des bateaux plus petits. Ce sont des usines de taille encore humaine : pour développer un projet on a un rapport direct avec le technicien principal de l’usine. Et l’on a affaire à des gens très compétents, très qualifiés. L’aluminium est un matériau délicat à travailler. Les soudeurs sur aluminium ont des qualifications beaucoup plus dures à passer que pour l’acier.
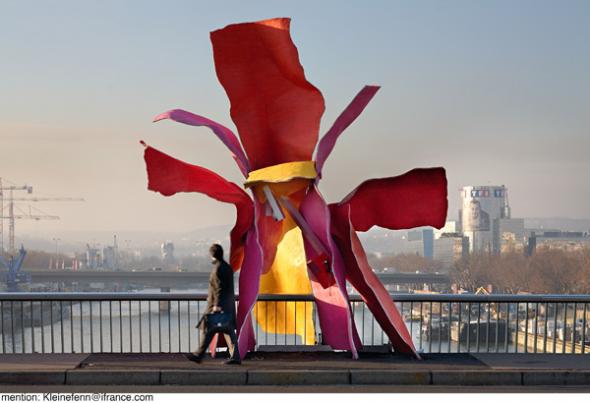
Oeuvre de Frank Gehry et Sophie Calle.
AMC : Un matériau aux multiples qualités, des entreprises qualifiées et à vous entendre souples et disponibles, comment se fait-il que des projets comme ceux que vous avez signalés ne sont pas plus nombreux ?
B.V. : Je crois d’abord qu’il y a encore une grande méconnaissance des qualités et des possibilités de l’aluminium. Cela tient au fait du cloisonnement des métiers. On a des métiers où l’aluminium est bien connu, utilisé très couramment. Par exemple les chantiers navals ont développé des technologies pour fabriquer des bateaux qui sont tout à fait intéressantes au plan économique. Il y a aussi les industriels liés au mobilier. Or le monde de l’architecture et de la construction n’est pas ou peu en contact avec ces industries. Cela n’est pas uniquement le fait des architectes. Les constructeurs sont aussi cloisonnés. Le charpentier métallique travaille avec l’acier et ne sait pas à priori utiliser l’aluminium. Le façadier lui connaît l’aluminium mais en tant que produit fini. Il ne fait que découper et sera réticent à le souder alors que le soudage de l’alu est tout à fait possible. Encore une fois les chantiers navals ne font qu’une seule chose, c’est souder l’aluminium.
Ce que nous nous faisons dans notre pratique au sein de notre bureau, T/E/S/S atelier d’ingénierie, c’est vraiment d’aller chercher justement ces compétences ailleurs pour les rapporter au bâtiment.
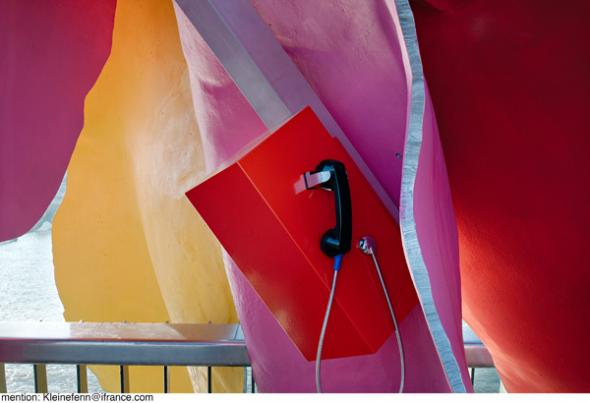